Discovering the Right Provider for Welding Inspection Madison: Key Considerations
Discovering the Right Provider for Welding Inspection Madison: Key Considerations
Blog Article
Checking Out Advanced Devices and Methods for Accurate Welding Examination
In the world of welding assessment, the search of accuracy and reliability is vital, stimulating the advancement of advanced devices and methods. Laser scanning developments and automatic evaluation systems, equipped with synthetic intelligence, are redefining the landscape by minimizing human mistake and improving safety actions.
Ultrasonic Evaluating Innovations
Ultrasonic screening advancements often stand for the forefront of innovations in welding evaluation innovations. These innovations have substantially enhanced the ability to find and evaluate stoppages within bonded frameworks, making certain enhanced honesty and security - Welding Inspection Madison. Ultrasonic screening uses high-frequency acoustic waves to penetrate products, providing detailed info about interior functions without causing damage. The current growths in this area have concentrated on raising accuracy, speed, and the capability to analyze intricate data.
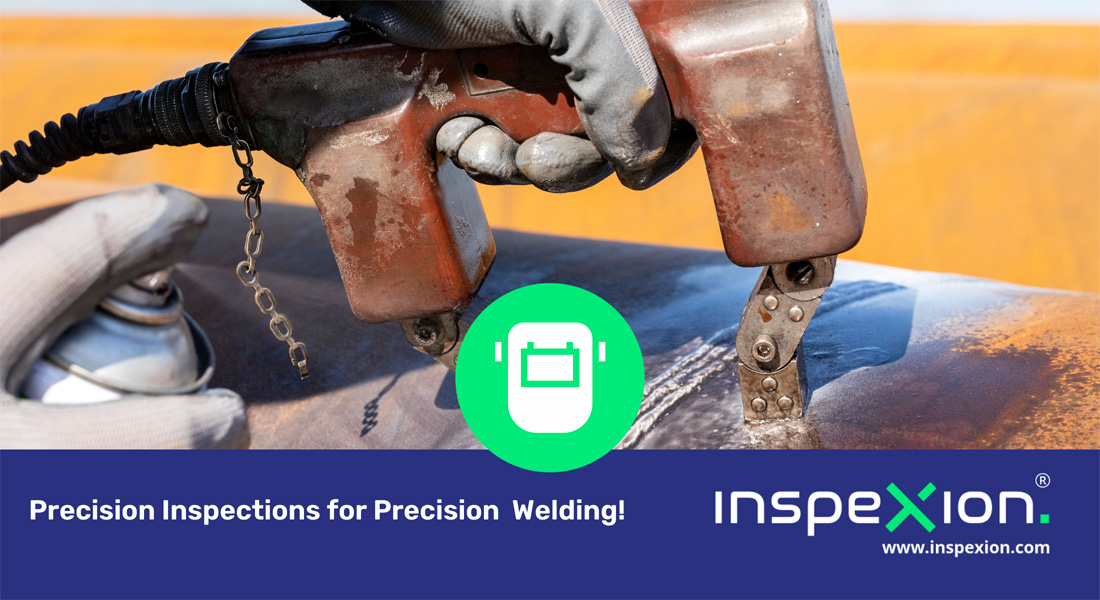
Furthermore, advancements in software algorithms for information evaluation have actually enhanced the precision of defect detection and sizing. Automated ultrasonic screening systems now supply high-resolution imaging, allowing comprehensive assessments of weld high quality. These systems are often incorporated with sophisticated visualization devices, which promote the interpretation of results.
Radiographic Examination Strategies
While ultrasonic testing advancements have set a high criterion in non-destructive exam, radiographic examination strategies proceed to play an indispensable function in welding assessment by offering unique insights right into product integrity. Radiographic screening (RT) uses using X-rays or gamma rays to permeate products, creating a radiograph that aesthetically represents the inner structure of a weld. This imaging ability is indispensable for detecting subsurface defects such as porosity, additions, and cracks that might not show up through surface evaluations.
The process involves positioning a radiation source on one side of the weld and a detector on the contrary side. Variants in material density and thickness impact the depletion of the rays, producing a different picture that specifically defines flaws. RT is specifically beneficial for inspecting intricate geometries and thick areas where various other techniques might fall brief.
In spite of its efficiency, radiographic examination should be carried out with strict adherence to safety methods due to the harmful nature of ionizing radiation. Furthermore, the analysis of radiographs needs experienced personnel, as the quality of the evaluation straight influences the integrity of the examination. Recurring innovations in digital radiography are enhancing photo clarity and analysis performance, strengthening RT's essential role in making certain weld top quality.
Laser Scanning Breakthroughs
Welcoming laser scanning modern technology in welding inspection has transformed the assessment of weld top quality and stability. Unlike conventional examination strategies, laser scanning offers rapid information acquisition, significantly boosting the efficiency and precision of weld analyses.
Laser scanning advancements have caused substantial renovations in identifying and detecting surface area flaws such as porosity, lack you can try this out of combination, and damages. The high-resolution data makes it possible for assessors to carry out extensive evaluations, making certain that welds meet stringent industry criteria. This approach supports the growth of digital documents, promoting long-term quality assurance and traceability.
Additionally, laser scanning innovation incorporates perfectly with software solutions designed for automated issue discovery and analysis. The resultant information can be easily shared and examined, advertising collaborative decision-making procedures. As sectors remain to demand greater standards for weld quality, laser scanning continues to be at the forefront, using unmatched accuracy and efficiency in welding assessment.
Automated Evaluation Systems
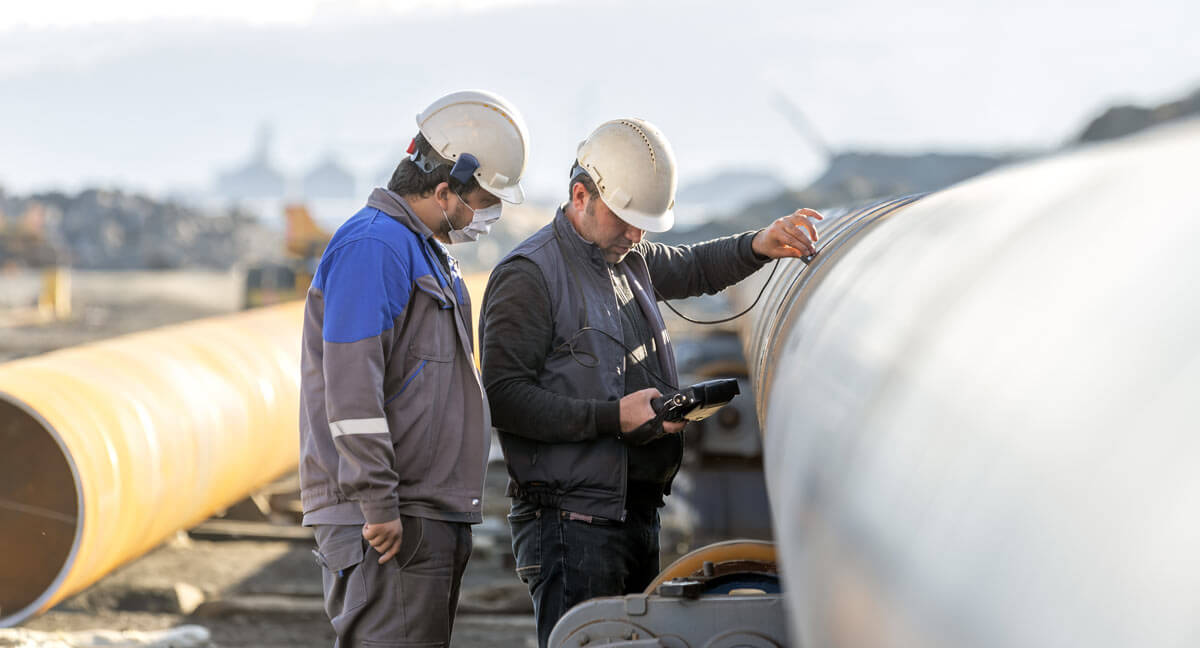
Automated evaluation systems offer the advantage of consistency, eliminating human error and subjectivity from the assessment process. They are created to operate in various environments, from production floorings to remote field websites, ensuring extensive protection. Welding Inspection Madison. These systems can be set to follow particular welding criteria and criteria, providing in-depth reports and documents for high quality control purposes
Furthermore, the integration of cloud-based platforms assists in the storage space and analysis of large amounts of assessment information. This enables trend evaluation and anticipating upkeep, permitting producers to attend to possible concerns before they escalate. The adoption of automatic inspection systems is an essential move in the direction of enhancing the reliability and performance of welding procedures in industrial applications.

Enhancing Security and Efficiency
A substantial element of improving security and effectiveness in welding inspection depends on the assimilation of ingenious technologies that enhance procedures and alleviate risks. The adoption of innovative non-destructive testing (NDT) methods, such as ultrasonic testing, phased selection ultrasonic screening (PAUT), and radiographic screening, plays a pivotal role in making certain architectural honesty without compromising the safety site link of the employees entailed. These techniques allow for extensive evaluations with marginal downtime, minimizing prospective risks related to standard techniques.
Moreover, the execution of real-time data analytics and device understanding algorithms has actually transformed the method inspection information is analyzed. By employing predictive analytics, prospective issues can be identified before they materialize right into vital failures, guaranteeing timely treatments and maintenance. This aggressive strategy significantly boosts operational performance and security in welding processes.
Furthermore, remote examination modern technologies, including drones and robot crawlers furnished with high-resolution cameras, allow inspectors to analyze hard-to-reach areas without subjecting them to dangerous conditions. This not only boosts assessment precision yet also decreases human danger. By leveraging these sophisticated devices and approaches, industries can accomplish higher safety and security standards and operational effectiveness, ultimately leading to even more reputable and sustainable welding examination practices.
Final Thought
The integration of sophisticated devices and techniques in welding evaluation considerably enhances flaw discovery and makes sure architectural stability. These advancements not only boost evaluation Recommended Reading performance however also contribute to improved security and top quality assurance in industrial welding applications.

Ultrasonic screening developments regularly represent the center of advancements in welding assessment modern technologies.While ultrasonic testing developments have actually set a high requirement in non-destructive evaluation, radiographic assessment techniques proceed to play an indispensable function in welding inspection by using unique understandings into product stability.Embracing laser scanning innovation in welding evaluation has changed the analysis of weld high quality and integrity. As industries proceed to require higher criteria for weld quality, laser scanning continues to be at the forefront, supplying unrivaled accuracy and effectiveness in welding evaluation.
Automated inspection systems offer the benefit of consistency, removing human error and subjectivity from the inspection procedure.
Report this page